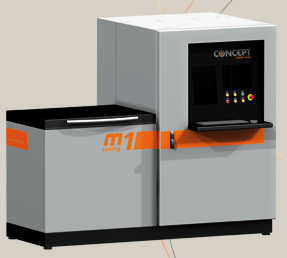
CONCEPT Laser GmbH has the machine solution for everyone who wants to start using LaserCUSING® straight away. Whether model makers, tool makers, die casters or service bureaux: M1 cusing is now available and offers a low-cost alternative to larger laser processing systems such as the M3 linear.
We have improved our tried and trusted machine technology. Customers can choose both the latest 200 W fibre laser and the proven and unique layering system. The machine concept: a laser station in which the LaserCUSING® process takes place and a handling station for pre- and post-processing.
The M1 cusing laser system is now available with a larger build envelope and is ideal for the production of small to medium-sized tool inserts and functional components.
Advantages:
200 W fibre laser. The M1 cusing has the latest generation of fibre laser technology. The high radiation quality allows the production of almost ideal component densities and thus mechanical properties that remain identical throughout the series.
Larger build envelope. Small to medium-sized components can now be manufactured up to a size of 250 x 250 x 250 mm (x, y, z).
Automatic powder exchange (optional). A mobile powderhandling system ensures both better accessibility to the machine and an automatic powder exchange. The personnel operating the M1 cusing have no direct contact with the metal powder.
Practical design. The M1 cusing has been designed so that the LaserCUSING® process takes place in the laser station under a controlled atmosphere. On completion of the component the construction process is comfortably postprocessed outside the laser station and a new order is prepared.
100 % density during the LaserCUSING® of one-component metallic powder materials. The exposure strategies have been further improved for the M1 cusing, allowing a significant increase in the construction rates and component quality.
Data:
LaserCUSING® materials Stainless steel CL 20ES (1.4404)
Hot-work steel CL 50WS (1.2709)
CL 60DG (1.2709)
Stainless hot-work steel CL 91RW
Nickel-based alloy CL 100NB (Inconel 718)
Cobalt-Chrome alloy CL 111COCR
(other materials on request)
Build envelope LaserCUSING® 250 x 250 x 250 mm ( x, y, z )
Layer thickness LaserCUSING® 20 - 80 μm
Production speed 2 - 10 cm3/h (depending on material)
Laser system Fibre laser 200W (cw)
Max. scanning speed 7 m/s
Focus diameter 70 - 200 μm
Reference clamping system EROWA, System 3R (others on request)
Connected loads Power consumption 7.4 kW
Power supply 3/N/PE AC 400V, 32A
Compressed air 5 bar
Inert gas supply 2 gas connections provided
N2 generator external ( optional )
Inert gas consumption < 1 m3/h
Dimensions 2362 x 1535 x 2308 mm ( W x D x H )
Weight 1500 kg
Operating conditions 15 - 35°C |