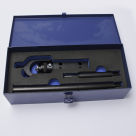
With the recent introduction of its E-series of honing machines, Delapena Honing Equipment has moved to de-mystify the honing process. Now, with Hone in a Tin the Cheltenham-based company is further simplifying the honing process.
The concept of Hone in a Tin is aimed at smaller subcontractors as well as larger companies that may get the occasional demand for producing honed bores. Depending on volumes their options up to now have been to further subcontract that operation, or if the volume demanded it look at investing in a honing machine. With Hone in a Tin as long as they have a spindle and a means of locating the component, they can hone bores.
Each ‘Tin’ comes complete with a hone head and drive shaft with the customer simply specifying the length and diameter of bore that needs to be honed. Bore diameters covered by this system can be between 25mm and 762m with four hone heads covering a range within that. The individual heads will be supplied with two sets of honing stones – one each for roughing and finishing. They can be supplied to suit the specific component requirements in terms of surface finish required and stock removal, for both roughing and finishing.
“We are confident that the Hone in a Tin concept will be warmly welcomed by small to medium sized subcontractor manufacturing companies, who now have a low cost route to honing, allowing them to maintain control of every aspect of the manufacturing process in-house,” says David Arthur, managing director of Delapena Honing Equipment. “As long as they have a spindle, which could be as simple as a pillar drill, they can now hone bores to precise tolerances, without making major capital investment.” |